Printing a Green Future- The Story of Eco-Friendly Ink Makers, EnNatura
This is a story of an intelligent, scalable innovation that has created a large impact. SparkTheRise, the campaign by Mahindra is an effort to bring such innovations to light when they're at a nascent stage and help them grow to their true potential. If you have an idea submit it here
KG Singh and Sidhartha Bhimania set up EnNatura. By outsourcing the manufacturing to small companies, they got by without making major capital investments. But getting companies to use the ink was another matter. They paid companies to use the product. The gamble paid off.
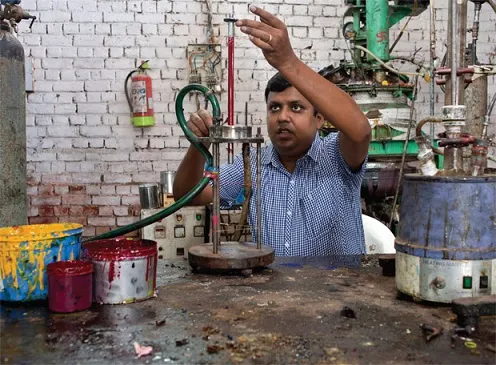
The Challenge
THE OFFSET printing business — think media, publishing, advertising and packaging, to name a few industries — consumes more than 3 million tonnes of hydrocarbon-based printing ink and chemicals, and emits over 5 lakh tonnes of volatile organic compounds (VOCs) annually. Apart from posing a serious threat to workers in the printing industry, VOCs are massive contributors to global warming. The key health and environmental challenge is posed by the petroleum component of ink, released as emissions during the drying and washing process. The resulting photochemical smog not only depletes the ozone layer, it can be linked to respiratory ailments in workers, including tuberculosis and an increased risk of cancer.
The Idea
KRISHNA GOPAL SINGH, a chemical engineer from IIT Delhi, and his friend Sidhartha Bhimania were brainstorming ideas for a start-up when they discussed it with their professor, who, it turned out, was working on ink. The solution seemed obvious: develop an ink that had negligible emissions. The challenge wasn’t just in developing eco-friendly ink though; it was in ensuring that this ink gave the same spectacular printing results and vivid colours as the conventional variety.
The real issue? Resin. The duo realised that they needed to develop their own resin to control emissions. Soon, they created a pH-sensitive resin from renewable feedstock, enabling them to create a biodegradable ink that causes zero emissions.
The next step? To do away with the use of hydrocarbon solvents. The unique chemical formulation of the ink also makes washing easier when recycling waste paper; the pH-sensitivity of the resin means the ink can be washed off with a mildly alkaline, aqueous wash solution, doing away with the need for hydrocarbon-based solutions that use kerosene. Not only does this dramatically reduce the environmental and energy footprint, it can be a game-changer in altering the economics of recycling. Singh estimates that washing costs are cut by as much as 85-90 percent compared with traditional methods.
The result? A fundamentally different printing process that has taken VOC emissions down to zero and makes recycling less expensive.
The Innovator
KG SINGH AND Sidhartha Bhimania set up EnNatura. By outsourcing the manufacturing to small companies, they got by without making major capital investments. But getting companies to use the ink was another matter. They paid companies to use the product. The gamble paid off. But they didn’t have enough money to produce quantities to meet the demand. They switched strategies by going to publishers and NGOs who were interested in green issues rather than printers themselves. With funding from the government and a venture capitalist, they have been able to get their dream off the ground.
The Impact
IT’S EARLY DAYS yet but having ironed out chemical issues, they have 10 printers now using their ink in varying quantities. “It’s a slow process,” says Singh. “Ink is a small cost vis-à-vis the cost of paper but its impact is very high; the wrong ink can lay waste very expensive paper. So adoption is slow and printers wait a long time, often months, to check how the ink deals with fading and other post-printing issues. But the fact that we have got 10 printers who now work with us is, in many ways, the end of stage 1 of the project. It’s time now for scale.”
The Way Forward
CHALLENGES OF SCALE are almost invariably linked to funding: no different for EnNatura. To meet the large-scale demand, they need to invest in manufacturing and marketing. “There’s actually been no barrier to trials,” says Singh. “People try the product easily enough. But to switch to using this in serious quantities requires commitment from printers. We have got the product right after trials and reformulations for around 18 months with printers. Now we need to look at the business and operations end of it.”
Submit your idea and SparkTheRise.
[The article has been reblogged ]