IISc has found an environmentally friendly way to recycle electronic waste
As per the United National Environmental Programme, there is about 50 million tonnes of electronic waste generated all over the world every year. In an endeavour to address this growing issue, researchers from the Indian Institute of Science (IISc) have found a method to recycle this humongous pile of e-waste in an environmentally friendly fashion. The method is also more efficient than those currently in use. 'Materials Today' published the results of the study.
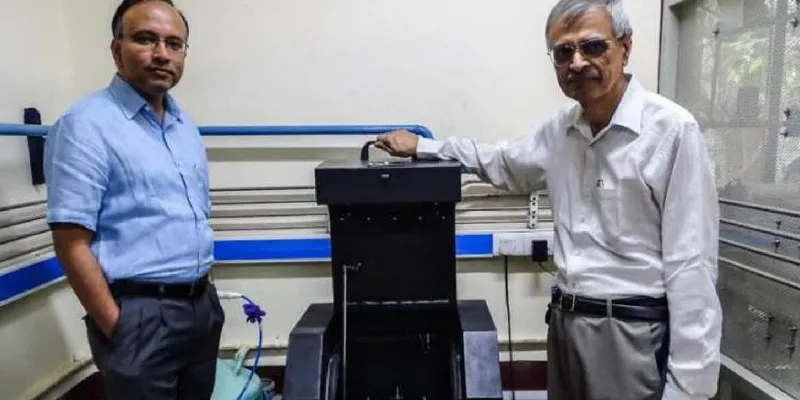
This new method involves the use of a ball mill at a very low temperature to reduce the electronic waste into nano-size particles. The temperature is very low, ranging from -50 to -150 degrees Celsius, which helps to eliminate any noxious emission. The e-waste is crushed into nano-size particles for around thirty minutes. In the process, the waste gets reduced to its constituent phases, and these crushed particles can then be separated without using any chemicals.
The idea for the method was thought of by Dr. Chandra Sekhar Tiwary from the Materials Engineering Department at IISc. According to The Hindu, Dr. Tiwary, the first author of the paper, said,
The behaviour of individual materials is different when they are pulverised at room temperature. While metal and oxides get mixed, the local temperature of polymer increases during grinding, and so the polymer melts instead of breaking. The polymer starts reacting with the rest of the components and forms a chunk. So we can’t separate the individual components.
According to Science Chronicle, Professor K. Chattopadhyay from the Materials Engineering Department, who is the corresponding author of paper, said,
The deformation behaviour at low temperature is very different from room temperature. There are two processes that happen when milling. The polymer material breaks but metals get welded, some sort of solid-state welding resulting in mixing; the welded metals again get broken during milling. At low temperature, mixing does not happen.
When crushed at room temperature, there is a lower limit to which the material can be reduced -- around 200 nano metres. However, in the case of low temperature ball milling, the material can be reduced to the size of 20-150 nano metres.
Liquid nitrogen is used to cool down the cryo-mill grinding chamber. The material is ground in a controlled inert atmosphere of argon gas with the help of a small hardened steel ball. It is done in an inert atmosphere to keep the interface clean.
Separation of components using gravity into individual classes is done by mixing the reduced fine powder into water. Two layers are formed, the top layer comprising of polymers that have low density and the bottom layer comprising of metals and oxides that are of similar size but different density. On further separation, the metals settle down at the bottom layer, while the oxides make up the top layer. Metals and oxides are then obtained as individual elements.
According to The Hindu, Professor Chattopadhyay said,
Our low-temperature milling separates the components into single phase components without using any chemicals, which is not possible using other techniques. Our process is scalable and is environment friendly, though it uses higher energy.
Do you have an interesting story to share? Please write to us at [email protected]. To stay updated with more positive news, please connect with us on Facebook and Twitter.