Here’s how developers can tap technology to build efficiency into the construction industry
Streamlining, monitoring, analysing, and reviewing the construction process with the help of technology can help bring in several efficiencies and savings.
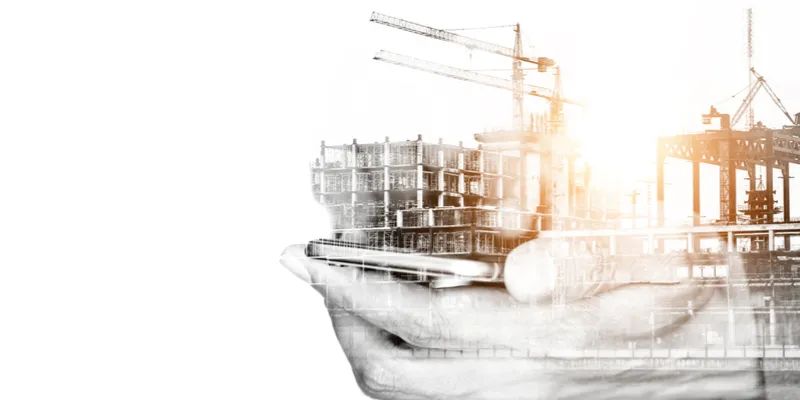
The Indian real estate market is expected to touch the US $180 billion by 2020, and the housing sector alone is expected to contribute about 11 percent to India’s GDP by the same time. Apart from its contribution to the economy, the construction industry is also an important source of employment for many people in India. It is, in fact, the second largest industry in India after agriculture.
But the construction industry in India works in an inefficient, ad-hoc manner. Much like agriculture, quality and efficiency issues plague the sector. The existing construction process has several built-in inefficiencies at every stage, right from procurement of materials to actual construction and quality control. On average, the wastage in the construction industry per square foot is nearly 80 percent more than what is considered best practice.
But current processes and protocols provide a tremendous opportunity for savings! Data analysed from 200-plus large to small residential projects, covering 30 million square feet of developed space in Tier I to III cities in India shows us that builders can realise savings of Rs 21 per square feet.
This number is significant when one juxtaposes this alongside the fact that profits are in the 8-9 percent margin in the construction industry. Even a 1 percent savings potential makes a big difference to the bottom line.
The cost of poor quality
In the residential construction segment, the Cost of Poor Quality (CoPQ) is an estimated Rs 33,000 crore on account of re-work and material cost. In addition to the material costs, the additional time needed by the labour force is a mind-boggling 5.3 million man-days, which ideally should have been gainfully used to ensure completion of the project on time. This includes additional penalties and finance charges that the project will attract due to the delays. RERA too is an important factor with respect to on-time completion and penalties builders have to bear for delaying delivery of units to the owners. In both scenarios, technology aids and abets greater transparency and accountability, and helps developers upgrade their construction processes.
The aggregate CoPQ is further broken down by category to provide key insights into the areas of savings. For example, Doors and Windows itself accounts for Rs 5.1 per square feet. Within this category, more than 60 percent of the wastage comes from two issues – “gap between shutter and frame” and “damage to the frame/shutter/fixture”. Obtaining such granularity of data of where the wastage is, in real time, will allow timely action to be taken to avoid greater losses.
Unlike several other sectors, the construction industry has remained something of a laggard when it comes to technology adoption. Despite the fact that 95 percent of the workforce and 90 percent of construction costs reside on the project site, almost all existing enterprise applications for construction cater to the office environment.
Technology touches only five percent of the workforce and has an impact on only 10 percent of the costs associated with construction.
How can tech make a difference?
To date, the big technological leap at the work site has been a shift from a paper-based project tracker to WhatsApp groups. Yes, WhatsApp. It certainly is an improvement, but far from an ideal replacement. WhatsApp allows easy sharing of information within a group, and also helps capture status updates via pictures. But think of a building project with multiple towers, coordinating various activities such as delivery of materials, fixing of doors and windows, inspection of completed work, and various other items. The limitation of WhatsApp becomes self-evident.
The obvious question that arises is: why has there been a delay in tech adoption in the construction industry? And a corollary to the question: why is it not on the labour force side of the business, where the most cost benefits can be realised?
Simple and SMART does it
The answer is simplicity. Any technology at the construction site has to be extremely simple to use, easy to cart around, and be as accessible as the sheaf of paper (and WhatsApp).
The simple answer is a ubiquitous “app” with an easy to use UI combining the power of paper and WhatsAppability of messages, and building into it the power of big data analysis. It’s the S-M-A-R-T (S- Streamline, M-Monitor, A- Analyse, R- Review, and T- Technology) approach to construction.
Streamlining, monitoring, analysing, and reviewing the construction process with the help of technology can help bring in several efficiencies. Streamlining allows sequencing of jobs, monitoring refers to ensuring a proper audit trail at every stage of construction (especially with the introduction of RERA), and analysis helps in keeping track of progress. Reviews help to reward or penalise the workforce based on how well they are meeting targets; with corrective actions based on feedback.
To illustrate: imagine the construction of a 10-storey apartment and one of the many jobs at the site, the fixing of the doors and windows (the #1 reason for wastage). Civil works have been completed, and doors installed. On the app, the job is marked complete, and an inspection is scheduled to ensure that all is in order. An alert for inspection is automatically added to the work order of the engineer in charge, as per the schedule of work. During the inspection, the engineer finds a snag and captures it with a time-stamped picture. Following this, an alert is set up for the contractor to fix the issue, labour pool to be assigned to make the correction, and a second inspection upon completion of the work is entered into the work orders at the site. The app allows engineers, contractors, and the labour pool to seamlessly streamline, monitor, analyse, and review. Multiply this activity by the 101 other job orders on site, and one gets a sense of the scale.
Aside from helping streamline jobs in real time, the collected data from the site is also able to forecast the average time taken for the completion of a particular activity, for example, tiling in an apartment. With actual information available from the site, the tech can extrapolate the time required to finish tiling for the whole floor and tower. Builders are alerted in advance, should there be a need for more contractor resources on that particular activity. This will help them catch up to what was scheduled originally and know whether they will be able to deliver on time.
Another big benefit of technology is the real-time dashboard. In the earlier days, estimating the progress of the project involved collating information from various engineers in charge of civil works, electricity, plumbing, and others. With the help of the app-based tech platform, this information will now be available in real time as it allows for daily monitoring of work orders on site.
The use of technology on the construction site can save 40 percent of an engineer’s time during any site inspection of activity, up to 40 percent savings in re-work, and up to 75 percent improvement in the quality of the end product through regular monitoring and actions taken.
Technology offers several great advantages to the construction industry. Leveraging it the right way can give a much-needed edge to builders to dominate the industry.
(Disclaimer: The views and opinions expressed in this article are those of the author and do not necessarily reflect the views of YourStory.)