How this startup is disrupting the manufacturing industry with its AI and IoT solutions
Bengaluru and San Francisco-based Lincode Labs is creating smart factory solutions to automate processes at factories to boost productivity and cut costs.
After the arrival of connected cars in the past decade, autonomous vehicles are set to become a reality. Similarly, the manufacturing industry is adopting technology to become more connected and autonomous. Companies are also talking about Industry 4.0, where real-time data enables factories to be independent, and help boost productivity and save costs. However, almost 80 percent of factories around the world are yet to be connected.
In order to automate the processes at factories, Rajesh Iyengar and Ritika Nigam founded
Labs in September 2017. The Bengaluru based startup uses Artificial Intelligence and Industrial IoT solutions to increase the profitability of companies in the manufacturing, healthcare, and fintech sectors.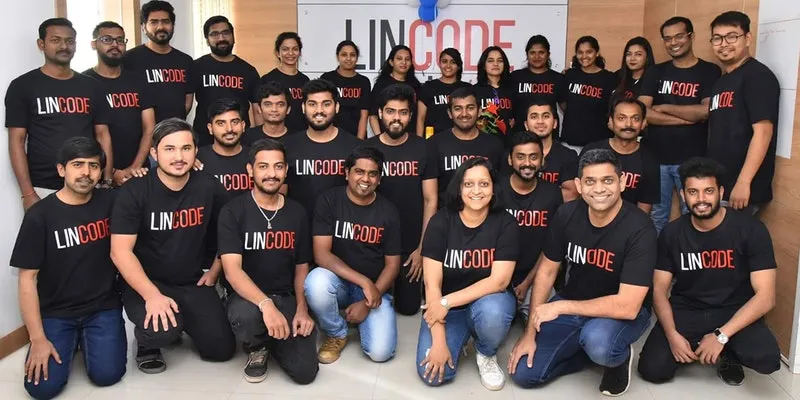
Lincode Labs team
“We help manufacturers automate visual inspection and improve overall equipment effectiveness (OEE) by identifying product defects using computer vision and artificial intelligence with the help of deep learning. This improves the accuracy of surface defect detection with greater precision, and easily integrates with existing manufacturing environments,” says Rajesh.
Lincode Labs has also created Smart Manufacturing, AI, AR, and Robotics Consortium (SMAARC), an ecosystem of industrial partners, to proliferate the future of manufacturing technology and innovation.
How it started?
Rajesh and Ritika had worked together previously. “While working together, our customers – all in the manufacturing sector – faced the same primary challenge - automating quality inspections to be faster, more reliable, and less expensive,” says Rajesh.
By the time Rajesh sold his previous startup in 2017, Ritika and he started building a strong partnership of loyalty and trust. They set out to solve the primary challenge of their former customers and built a team, developed the product, and started growing the business in India.
In 2018, the duo travelled to the Silicon Valley to expand the brand internationally. And here, they met their third co-founder, Eric Malis, an established businessman, startup advisor, and attorney, and they together incorporated Lincode Labs in the United States, and started building their global operations. The startup currently has a team size of 40.
How it works?
Even the most expensive systems in companies require people to pre-program it. While algorithmic-based processing advances accuracy and speed, the system still requires human intervention.
Lincode Labs claims it was set up to solve this very problem. It helps factories with visual inspection of products, surface defect detection, and to save time in production schedules by providing warehouse and employee automation products.
For this, the startup first obtains data from product samples by using complex algorithms to understand their characteristics. It then deploys the solution ‘on-premise’ or via the ‘cloud’, based on the customer requirements to solve problems.
The product uses a combination of user-based algorithms, deep learning models, and experiential innovations to enable manufacturers to add an inspection station for the selected processor product without the need for expensive hardware.
“We use advanced AI-based computer vision technology to identify defects that need not be pre-programmed. We can work with companies in the manufacturing supply chain to improve their visual inspection processes. We provide B2B solutions to ensure visual quality inspection at intermittent production stages and ensure the final output is faster, more reliable, and cost effective,” says Rajesh.
The first client
The founders claim some of their first clients were customers from their previous company who were looking for a solution.
“Our first major client came through one of our channel partners. We were introduced to a large automotive manufacturer, which had been struggling to identify subtle defects on its export lines and eliminate the shipment of defective parts to its customers,” says Rajesh.
“We started with some of their more complicated parts and quickly proved our capabilities. Now, we have over 120 inspection stations identifying and classifying over 2,200 of their products, measuring various dimensions, and inspecting defects across multiple production lines,” he says.
Today, Lincode claims to be having around 40 clients globally. While some of its clients are from the plastic and metals industry, it also has clients from the automotive, electronics, pharmaceutical, and polymer industries. Some of their clients include Stanley and GE.
Investment and revenues
To begin with, Rajesh invested around Rs 2 crore in the startup. But he says, the investment has come at the cost of opportunity as well as personal sacrifice.
“To build Lincode, I gave up the job at a semi-conductor company, which was ready to pay me over one crore annually. Working late nights, I have also missed moments with my family in order to build what I know will eventually pay off for them and the industry as a whole,” he says.
Lincode Labs makes money by helping customers achieve targets. Accordingly, the startup charges its customers based on the number of inspection stations deployed, complexity of the applicable analysis, and the number of unique parts to be inspected.
The startup claims it is currently revenue positive. As the startup expands key relationships and further develops its product line, it also plans to raise more money.
The market and future
As companies around the world are becoming more comfortable with Industry 4.0 and smart factory solutions, the appetite for how deep learning can revolutionise manufacturing is growing.
According to MarketsandMarkets, Artificial Intelligence in manufacturing market is expected to grow from $1 billion in 2018 to $17.2 billion by 2025 at a CAGR of 49.5 percent during the forecast period. The huge availability of Big Data and increase in venture capital investments are the factors fuelling the growth of the AI in manufacturing market.
The startup claims it is currently focussed on delivering the best possible visual inspection solutions for industries.
Over the next 18 months, Lincode Labs plans to expand the number of deployments of its leading solutions at factories. It currently competes with companies like FogHorn, Gem, and InfluxData.
The startup is expanding R&D efforts on new product deployments to address the emerging challenges faced by manufacturers. It is also expanding its patent portfolio as it develops new products and processes.
(Edited by Megha Reddy)