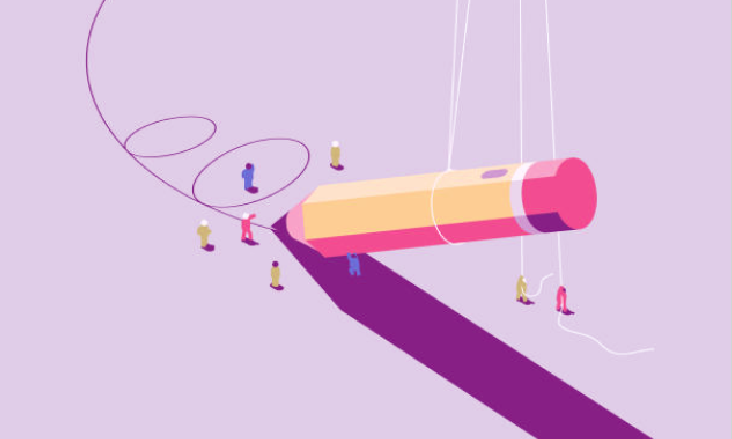
Top 7 Reasons For Wastage In Manufacturing
Don’t let waste eat up your profits. Manage and reduce it efficiently using an ERP solution and see its direct effect on your bottom line.
Friday October 14, 2016,
5 min Read
One of the key parameters for the businesses today is achieving early ROI. Organizations are under tremendous pressure from the management to increase the rate of return on investment to realize profits. Traditionally, ROI was linked to ‘cost savings’ and, it’s true till today also. Although there are other dimensions of ROI too, like customer satisfaction, brand differentiation, business growth, etc., that help drive increased revenue. But, the goal is always to drive measurable hard-cash, that too quickly; achievable majorly through cutting costs.
Along the length and breadth of the organization, there exists a number of elements that become the base of cost cutting. However, of these, there exists one element that mostly goes unseen by the decision makers and that’s ‘Waste’. If waste is recognized properly, handled efficiently and controlled substantially, its surprising effects can be seen clearly on the bottom line.
Below are the top seven reasons why the wastage occurs in an organization and how it directly or indirectly impacts the company’s Return on Investments. It is essential for the organizations to control such wastages in order to raise profits.
Over Stocking
Agreed, that having a large amount of inventory on-hand saves you from running out, but it brings along a number of disadvantages too. Caused by over buying to leverage a lucrative discount, or fluctuation in demand, or shift in trend, this surplus inventory, whether raw material or finished product, occupies the warehouse space resulting in additional rents, maintenance and handling costs. Some businesses have goods that, if not used within a specified time, tend to deteriorate, perish or lose its effectiveness, resulting in waste. Raw material over stock can be consumed by speeding up production, but finished good over-stock can lead to waste, if not sold at the right time.
By stocking adequate quantities and efficiently utilizing space, companies can directly cut down waste and save heavily on the rents, maintenance costs, electricity and similar overheads.
Inadequate or Obsolete Manufacturing Processes
Process industry is about mixing, grinding, heating and changing of forms. There’s a certain amount of waste incurred during the manufacturing process that cannot be avoided; for e.g., weight lost in pealing of vegetables, material left stuck in the equipment, evaporation, and a number of such kinds. However, the key is to identify where the waste is occurring. This helps chalking-out ways in which they can be minimized, through innovation, new age equipment and technology.
Over Production
Over production causes inadequate use of personnel, setup and materials. It also leads to unnecessary accumulation of goods on the production floor, which are difficult to manage. In absence of proper planning and scheduling, heaps of useless inventory items build up and ultimately, does not result in something productive, but only blocks money and space. If this money is timely freed up, it can be put to business driving activities.
Defected or Low Quality Goods
Defected or low quality goods are produced when inefficient manufacturing processes are practiced or when proper manufacturing instructions are not followed. An additional cost is incurred for rework, correction and managing scrap, which eventually leads to further shrinking of the bottom line and delayed ROI. In order to minimize such wastage, manufacturers should follow good manufacturing practices, apply quality checks on all processes and products, and continually inspect the production process.
Time Wastage Due to Lack of Information Flow
Time is money!!! It is very common to observe production or delivery halts in the absence of the right information. It may also occur due to improper channels or maybe in the absence of a single database source. Halts or delays may result in cancellation of the orders leading to stock add-up and thus, wastage. Such type of delays also hamper the market position and customer experience suffers too.
Wastage of Resources
The resources not optimally utilized are actually wasted. This generally happens due to the lack of collaboration, visibility and tracking. If a personnel or machinery is idle, it becomes an overhead of the company and further shrinks the margins.
Lack of traceability
Lack of traceability across and within your warehouses is yet another reason leading to waste. Typically, in the absence of bi-directional traceability, it becomes difficult to identify items close to expiry, expired or damaged in your warehouses. Even in the cases of recalls, inefficient traceability results in delay in taking corrective action. Consequently, production of the contaminated products is not halted timely, and this leads to wastage.
Putting It All Together
Identifying these wastes is essential, but it’s just one piece of the puzzle. The trick lies in managing and controlling it, possible incredibly through an Enterprise Resource Planning solution. An ERP offers impressive inventory management that enables proper handling, segregation and tracking of inventory based on a number of factors including shelf life, expiry, quarantine, etc. Its efficient planning module eliminates the chances of overstock and understock helping you stock just the right levels of inventory.
Bi-directional traceability and faster recalls offered by an ERP, provides tracking information at the touch of fingertips of everyone who needs it and the way they need it. Quality Control and Assurance features of ERP, ensure receipt, issue and production of desired quality goods. By providing powerful data and deep insights into all operations and processes, it helps utilizing resources to fullest while ensuring their complete collaboration. These and many more capabilities provided by ERP helps reduce waste which is otherwise linked to inefficiency, higher overheads, shrinking profits and ultimately delayed ROI.
Many manufacturing companies are now adopting ERP to identify and manage waste in order to enhance ROI.