Israeli startup 3DSignals uses sound to remotely monitor manufacturing and industrial equipment
Using acoustic data isn’t exactly a new technology. The innovative aspect of 3DSignals is the use of data that stems purely from the sound emitted from machines to the air around them.
The idea for 3DSignals was born on a train ride. Amnon was traveling in the UK when suddenly there was a very loud, alarming noise — one that made everyone stop what they were doing and wonder if they should hold onto something. The noise passed and everything was okay. He sat there thinking if an experienced train engineer had been there, he or she would probably be able to tell almost instantly from the noise what the problem was. More importantly, that expert could easily determine whether it was a sign of danger and how to fix it.
Together with two friends (experienced engineers), Amnon started to work on this idea of a sound-based ultrasonic remote asset monitoring and predictive maintenance platform. After developing the technology, the team tested it at a steel production plant. It didn’t take very long for the system to detect meaningful anomalies and save the factory hundreds of thousands of dollars by preventing unpredicted downtime. Six months after beginning the experiment, the team members quit their jobs and formed the company 3DSignals with their first design partner.
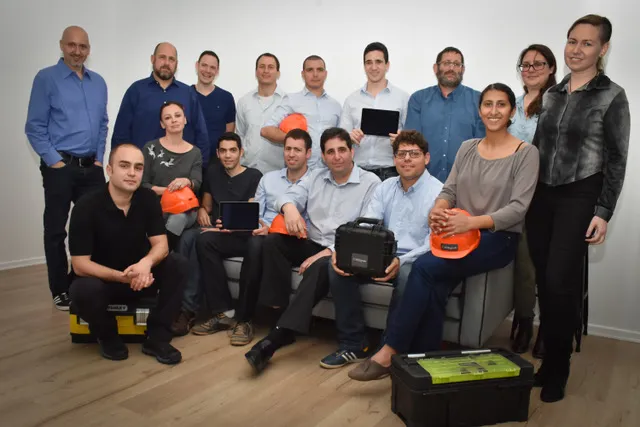
3DSignals (3DS) is a startup that uses cognitive computing and predictive analytics to prevent machine failure with acoustic sensors using algorithms. 3DS specialises in the application of sound-based predictive maintenance for industrial and manufacturing equipment. In the case of machine predictive maintenance, sound has excellent potential to identify anomalies because it’s easy for humans to understand — even if they are not physically near the machine. An anomaly in sound can be localised to its source after identified. With 3DSignals’ proprietary hardware and deep learning software system, customers listen to their machines with ultrasonic sensors, anticipate problems with real-time alerts, and reduce unplanned downtime with predictive analytics.
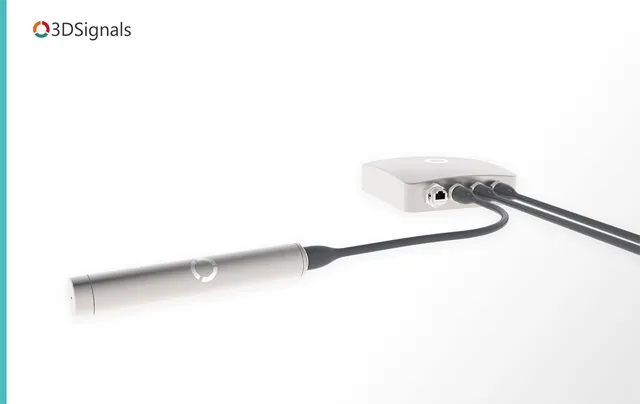
Using acoustic data isn’t exactly a new technology. The innovative aspect of 3DSignals is the use of data that stems purely from the sound emitted from machines to the air around them. The technologies that 3DSignals has introduced include ultrasonic sensors developed specifically for harsh industrial environments, as well as innovative deep learning predictive analytics software that learns to recognise specific acoustic signatures.
“For example, we can monitor a mechanical bearing subjected to extreme dynamic stress. When the first crack appears, the bearing will produce a unique ultrasonic pattern that indicates trouble ahead. 3DSignals’ system identifies and preemptively alerts operators of various failure states including bearing friction, shaft misalignment, blocked filters, lack of lubrication and others before they become a detriment to the machinery,” says Amnon Shenfeld, Co-founder and CEO of 3DSignals, explaining a use case.
Currently, 3DSignals works with a variety of industrial, manufacturing and power plant processes. One of their early successes was in the steel industry. The startup worked with a leading metal and steel service and processing company that distributes over 300,000 tons of metal worth $300 million per year. The company fabricates carbon steel tubes in a dedicated mill running 3 ERW production lines with machinery by Seuthe, Fives OTO Mills and MTM Tube Mills. Pipe manufacturing is known to suffer an average of 30-percent downtime, but this mass-production company was losing an alarming amount of money due to downtime reaching 53 percent. Two months after 3DSignals sensors were deployed, the mill’s three production lines had already saved the company $60,000 per line, compared to the same two months a year prior. The biggest benefit was an 80-percent drop in human operator errors due to the newly installed condition displays.
“We see huge growth potential moving forward. Today, there are many millions of industrial assets out there that are not yet modernised. Similarly, to how the e-commerce revolution forever changed retail, the smart industry revolution is about to disrupt conservative manufacturing industries. By some estimates there are 60 million machines in factories throughout the world and 90 percent are not connected. Meanwhile, 70 percent of the machines are more than 15 years old,” says Amnon on plans to expand their services globally.
“Sound monitoring offers a quick and painless method to upgrade old assets in factories and plants across multiple sectors without mounds of equipment or challenging integrations with legacy controllers and networks. Based on this growing market opportunity, we seek to democratise sound as a meaningful tool serving predictive maintenance needs, as well as operational efficiency and safety applications.”
Website: https://www.3dsig.com/