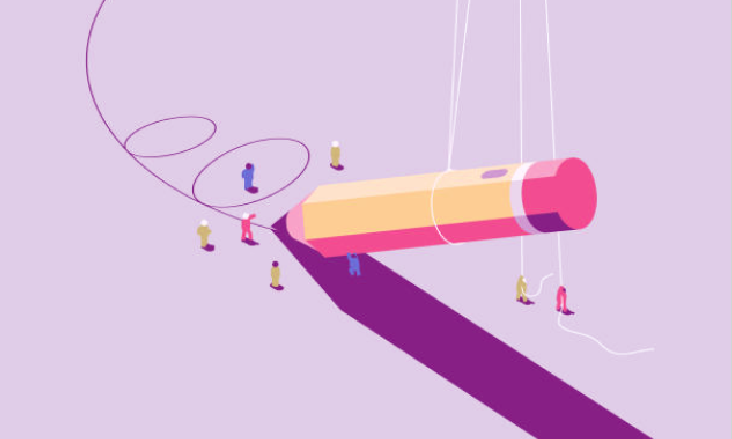
Is it Important To Test Rubber Goods?
Here is a very simple sounding question and the answer to it is simply, Yes!
It is necessary to test rubber goods to ensure electrical safety. First of all, let’s discuss why products made of rubber are used to deal with electrical appliances. Rubber has the least amount of conductivity and therefore, it is a poor conductor of electricity which means electric current cannot flow through rubber. This makes the recipient wearing rubber gloves or sleeves etc. safe if some electric failure happens. The average annual fatality rate of people working in power lines has been reduced to quite an extent because of the use of rubber products. However, this does not mean that once the rubber product is made, its ready for use. There are many levels of rubber testing involved to ensure that these products can provide the safety and durability which is expected of them. The process of rubber testing is a bit expensive but it is simply worth many lives that we can save by following this process. After all, you cannot put a price on life.
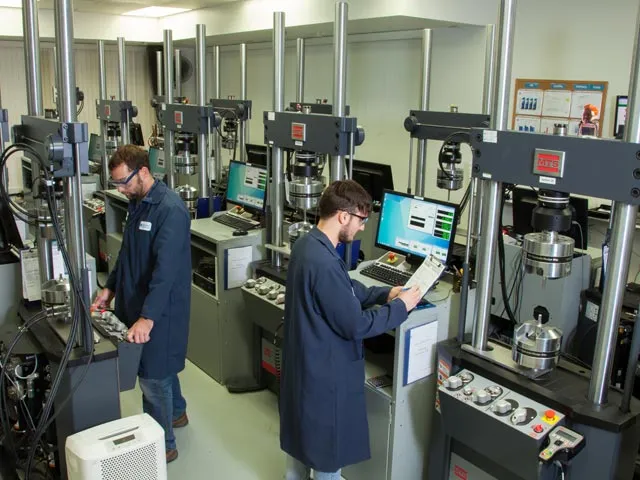
process of rubber testing
Below are the seven steps involved in rubber testing that ensures the quality of rubber products –
1. Cleaning – This step involves cleaning of rubber products from both inside and outside. Any kind of unwanted entity, dirt or stamp on the rubber is removed in the test labs. After these rubber goods are completely devoid of any conductive element, they are sent for visual inspection. Do not forget to dry out the goods before sending them for inspection.
2. Visual Inspection – This step is carried out by an expert inspector. To the naked eye, the goods might seem to be in a good state however, they may not be. Therefore, inflation and rolling are performed on them and post that they are scanned again. If punctures, cracks, scratches are present on the surface, they are not eligible for the next step.
3. Electrical testing – In this step, the rubber product is exposed to various degrees of electrical voltage depending on its class. If it withstands the voltage, it passes the test to qualify for the next step and in case a hole burns due to heat, the product is disqualified.
4. Certification – If the goods pass both the visual inspection and the electrical testing, it achieves a certification. This certification proves that this rubber good of the respective class is safe to use and can withstand damage in case of an electric failure.
5. Date Stamping – After being certified, the rubber good is stamped with an ink which does not fade away. The details that are stamped on the product are – testing date, expiration date, class of rubber, max. voltage it can be used for and the name of the lab in which it is tested in. This helps the user to know the complete information about the rubber good they are using.
6. Packing – After the stamps dry off, talc powder is sprinkled and dusted on rubber gloves and sleeves so that the powder can absorb any kind of moisture present. Further, they are heat sealed in plastic bags and are made ready for shipping.
7. Shipping – Solid protection is provided while shipping these rubber goods. They should not be crushed, folded or tampered with. Thus they are packed in firm cases with extra protection.
The fact that these rubber products will be used in highly hazardous working conditions, Rubber testing is extremely necessary. These small products are what stand between a life threatening accident and the workers. Thus providing the high quality, tested safety gear to your workforce is a part of good infrastructure.