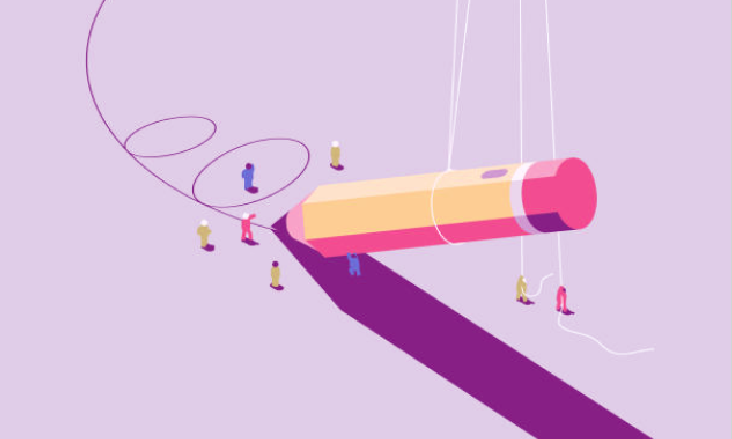
A Strategical Framework for Digital Transformation in Small Scale Manufacturing Firms, in the Industry 4.0 Scenario
Micro, Small & Medium Enterprises play an important role in the economic growth of any country. Many huge corporate houses of today began as a small enterprise when they were founded. Dell, Hewlett Packard, Apple, IKEA are examples of corporate behemoths , having/ which had in house manufacturing capabilities, which were founded as a small businesses.
Similarly , In India , there are a few companies in the manufacturing sector , which began as SME /Startups before growing big- For example: Packaged Foods Manufacturer-Balaji Wafers, Tech enabled mattress manufacturer- Wakefit have had humble beginnings- either as an SME or a Start up. Ministry of Micro, Small and Medium Enterprises, Government of India classifies a company as a micro enterprise, if the total investment in plant and machinery does not exceed 2.5 Million INR (Indian Rupees), a small enterprise if the total investment does not exceed 50 million INR and a medium sized enterprise, if the total investment does not exceed 100 million INR.
According to the Confederation of Indian Industries, there are 63.4 million MSMEs in India, contributing to 6% of the country's manufacturing GDP, 24% of the country's service GDP, 45 % of India's exports. MSMEs also provide employment to more than 120 million people and have been able to maintain consistent growth rates of close to 10%, thus forming the nation's economic backbone.
However, at the same time, there are a few unique challenges which MSMEs in manufacturing sectors face, which makes it difficult for them to adopt digital manufacturing and industry 4.0 related practices. In my opinion, MSMEs face 3 common challenges ,which are outlined below:
- Liquidity Risk and Cash flow maintenance: Many SMEs, especially those operating with a B2B Business model, often sell their products on credit of minimum of 30-90 days. Furthermore, they operate on strict cash flow margins, making it difficult for significant investments required for upgrading technology. Similarily MSMEs operating on B2C models constantly face the challenge to stand apart in the market and invest heavily in marketing.
- Manual Intervention and Mistake Proofing: The penetration of automation is often less, in many SMEs and most of the manufacturing processes have a high percentage of manual intervention either in their operations, or in inspection activities. While lean manufacturing concepts like mistake proofing, PokaYoke etc are being adopted, the effect of adoption is often very less compared to bigger manufacturing firms. This often leads to improper process standardization which may have direct impact on the product quality.
- Availability of Skilled Workforce: The tight cash margins, often force many MSMEs to adopt for contract staffing, making it difficult for the organization to invest in training programs required to Up-skill and sustain staff to work and operate in a higher technology enabled environment.
Given the nature of operations which these companies face, effective utilization of digital transformation and other concepts which fall under the umbrella of Industry 4.0 can help in realizing better working efficiencies across all fronts such as quality, productivity etc . However given the unique challenges faced by MSMEs in manufacturing, a well planned adopting digital manufacturing and industry 4.0 practices requires a well planned strategical approach.
A Strategical framework for implementing the same, incorporating the existing lean methodologies is explained in this article.
1561828514862.jpg?fm=png&auto=format)
- Evaluating and understanding the existing scenario within the company: Any MSME which wants to embark on a quest to transform itself has to develop a deep understanding of the nature of operations in the Shop floor and map the value addition expected.
- This is very much similar to the lean approach of Genchi Gembutsu, meaning " Go & See" in Japanese, which involves going to the shop-floor and observing the process happen. How much ever well documented processes are, there will be few elements of work which are not documented, which often, only come to the limelight in detailed process audits and for which the inputs of the operating associates & workers is crucial.
- Developing a value stream map: While traditional value stream maps focus more on the production data such as cycle time, production rate, Takt etc, here a key necessity here is to capture the information systems required sufficiently (such as product and process traceability mapping), across the entire value stream from stores to the shop-floor to despatch.
- A few questions which are to be considered here are : Is the working associate filling a lot of manual records, which make it difficult to trace product traceability? Can repetitive operations be automated for ensuring that associates are loaded optimally? Can softwares / Online process Control Systems and data capturing systems be used to eliminate manual entry to make process more robust?
- In addition to this, other tools such as Standardized work combination table, ECRS ( (Eliminate, Combine, Re-arrange, Simplify) Charts, Reverse FMEAs, Process Audits are important for identifying the opportunities for embarking on a transformation.
2. Adopting the Kaizen Approach to Implementing the Transformation:
- While, it may often be tempting for companies to take a deep plunge into the pool of digital transformation, a cautious and a well planned approach, with improvements happening in small increments is often the best method for implementing digital transformation strategies for MSMEs.
- Phased implementation of improvement programs will ensure that operations are not disrupted and hence the cash flows are not impacted , thereby minimizing risk.
3. Leveraging the Power of Technology in a smart way:
- Power of Low Cost Automation: Low cost automation solutions for the shop-floors, coupled with elements of automation such as sensors can prove a better return on investment than regular automation, for operations which have a high manual work content. Low cost automation techniques are typically carried out in house using very less investment and may often involve re-use of available components, scrap packaging etc . Low Cost Automation techniques, may also involve out of the box thinking such as doing away with traditional automation elements such as heavy power consuming motors, robots etc. For example, a gravity conveyor, along with a sensor for recognizing the component presence can be used instead of an expensive pick and place robot. Expensive PLCs can be replaced by PCs wherever possible, hardwire logic can be used.
- Power of Visualization: Visualization dashboards can often be created using softwares such as Power BI, Tableau etc in an easy way at low cost . Digital Dashboards can serve as a primary form of control in the shop-floor and can effectively replace traditional And-On Signage, traditional production monitoring board. Further, when integrated with dynamic databases, real time production data can be seamlessly providing better insights for visual control, effectively forming the best method of control.
- Power of Cloud Computing and SaaS: Having an in-house server system and an IT Team is not often beyond the economic scope for MSMEs. The power of Cloud Computing and SaS can be harnessed here, to create a superior IT enabled manufacturing environment. Compared to legacy systems which may charge a hefty installation fees and annual maintenance fees, cloud enabled systems often come as low initial costs, pay as you use billing models. Examples of Cloud Based ERP Systems include Ramco ERP on Cloud, SAP-Cloud Platform etc. An Example of Cloud Based PLM systems is PTC Windchill SaaS. This is also aided by cheaper internet prices in recent years. Furthermore, with the advent of cloud computing, software updates to avoid obsolescence has become easier.
- Power of Analytics and Artificial Intelligence: MSMEs, predominantly operating on a B2C model , facing order uncertainties can use predictive analytics and artificial intelligence for budgeting, predicting customer pull and hence balancing production and inventory. Similarly, maintenance and OEE data can be used for predicting reliability of machines and hence forming curated maintenance plans.
4. Leveraging the Power of Outsourcing and Collaboration: MSMEs most often may not have sufficient resources or the time to carry forward business transformations themselves. A collaborative vendor, often another MSME maybe in a position to provide better pricing compared to a full scale corporate services provided. With many big conglomerates migrating towards the usage vendor portals and vendor scorecard, MSMEs can gain insight into their performance, by using their respective customer portals.
Additionally, The Ministry of Micro, Small and Medium Enterprises has also launched a portal for PSUs to monitor procurement from MSMEs - MSME Sambandh, a placement and job portal for recruitment- MSME Sampark .
5. Leveraging the power of their size: A common factor which hampers organizational agility for faster business transformation is the size of an organization. MSMEs being smaller,with fewer employees and a smaller global footprint, can use their size as an advantage for embracing digital transformation better and faster. Lesser the number of employees means lesser the organizational resistance, by and large, making it easier for a cultural transformation among employees, for embracing a digital future.
6. Training , Education and Knowledge Transfer: A key to ensuring successful knowledge transfer is to document the process of transformation as much as possible, maintaining a list of things gone right and things gone wrong. Key approaches and nuances can be integrated with regularized training modules developed.
7. Sustenance and Analysis: Sustaining digital transformation improvements carried out is vital. Like any improvements carried out, the same Deming Wheel Approach can be carried out in this regard. Process Audits, Information audits , continual improvements in the form of system upgrades are crucial for sustenance and effectiveness monitoring
References:
- Ministry of Micro, Small and Medium Enterprises: Definition of MSME:
- How did Wakefit earn Rs 114 Cr revenue in 3 years? By helping customers get a good night's sleep- Article in Yourstory on April 05th, 2019: By Athira Nair and Apurva P. L
- CII Page on MSMEs.
- Picture Credit: MSME AS MANUFACTURING UNITS FOR INTERNATIONAL ENTERPRISES, published in Business Economics Website, on 30th March 2017, article written by Anustup Roy Barman
- Low Cost Automation- A Case Study by Mohan Kumar KG, published in Efficient Manufacturing on May 23rd 2017
Disclaimer: The Views of the author are that of his own. The author is not associated with any of the organizations mentioned in this article, but has merely mentioned their names to quote as examples ( taken from popularly available literature and articles on the net). This article was published by the author in his Linked-In Page