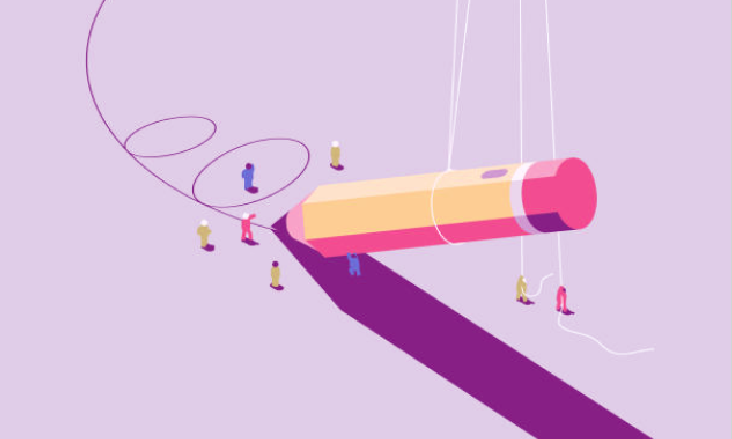
The Operations of Strategy across a Supply Chain
The role of operationalising your strategy in your supply chain.
Quite a mouthful of a heading, isn't it? Well, in due fairness a supply chain is not usually looked upon with the need for a budgeting exercise and neither a strategic plan for an upcoming financial year (kudos to you if you already do so!)
Well, a supply chain in essence is a function that ensures the flow of goods/services and information to ensure what the customer needs is met. (now you would wonder isn't that a sales/marketing team's headache?) Well, no. Their aim is to ensure that the 'what' (the good/service) is pushed for a sale to the customer. New product requirements are assessed by the same market research team and it ought to be relayed back to the design as well as the entire supply chain team.
So, what is the 'operation' of 'strategy' in the chain? When I mention 'operation' I imply the 'role' of strategy in a supply chain. Now what's strategy, you'd ask me? It's basically a plan you take up to achieve a desired goal. Now, here's the fun part-what would the supply chain's goal be? Taking a cue from the reknowned book 'The Goal':-To make money by increasing net profit, while simultaneously increasing return on investment and simultaneously increasing cash flow.
Now you would wonder isn't this a firm's goal? Yes it is, but a firm runs on the simple principle of either production of goods or offering services that are meant for a customer (rather many customers) so as to arrive at the desired cash register ringing in. Now, this depends fundamentally on the internal operations from make to deliver and customer handling (and vice versa).
Yes it is in essence how precise the quality is, optimised the flow of process is, the reliability and integrity displayed in your commitments towards deliverables to your customer as well as your internal deliverables. Now think of the goal in a purely business fashion as each sub-function's goal. So let's say Customer A requires Product P by date D and is monetarily worth INR (or any other currency) 100 (internally the INR 100, should already be a mark up on the costs so that there is a profit margin rendered in).
Once this is in place with a time-stamp, it is in fact very easy to ensure how each sub-function ought to prioritise their workflows. Moving backward across the chain the strategic controls are on timeliness, so the sales function needs to deliver the product to customer A and thus keeps a check on whether it is ready with the packaging team. Now the packaging is only possible when the product is ready and also when the materials required to input into the packaging are made available (labels, wraps, branding material, price tags for consumer products while in the case of heavy engineering and automobiles this is replaced with a direct door delivery or even a limited packing and bubble-wrap on the seats). So this team needs to ensure these materials as well as the necessary product is ready for the aesthetics to be in place.
What happens next? The manufacturing team ensures the product is ready (and when I say ready it implies the product is made structurally and functionally with the necessary raw materials and is also approved as per quality standards), now this is again dependent on the availability of materials on the assembly line. Any amount of idle time of an operator because of machine idle times and that of because of lack of materials would imply a delay in the production of the good.
Now going one step behind, the materials availability are a direct function of procurement teams' negotiating capabilities and more of a reflection of the vendor's deliverability as well as transporter's timeliness. Once all this comes together, is when the product finally reaches the customer. However, things don't stop there-it's back from the customer for re-work/an exchange or return.
So what's the operations of strategy in a supply chain? In a nutshell it's the role to affix a time-bound goal that stems from the monetary impact as well as the goal is measurable and achievable for each sub-function and function at large.
How can that be achieved? Well more on this in the next post: the metrics and the methods across the supply chain to ensure its strategy is operationalised and executed.