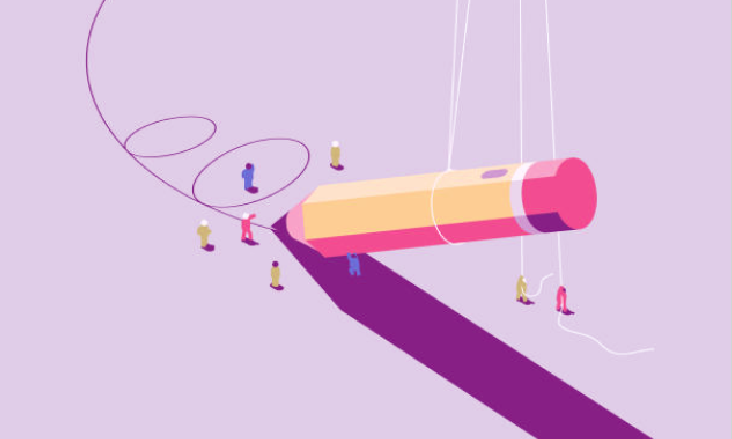
Things every manufacturer should know about injection moulding
Injection moulding is an inventive technique of manufacturing parts in immense volume. This technique is common in mass-production processes that specialize in creating the same part thousands or millions of times repeatedly. Apart from being simple and dependable, injection moulding is arguably one of the most efficient processes for mass production of parts.
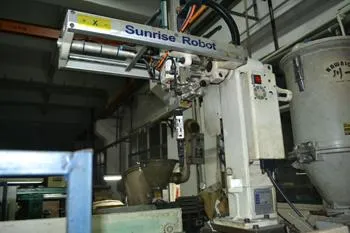
How does the process work?
The process entails converting small pellets of material into a hot liquid by heating. The hot molten liquid is then forced through an outlet and into a mould. The internal cavity of the mould is usually the negative of the part that is being produced. After cooling off the molten parts, elector pins are used to remove them from the mould.
Why should you use injection moulding to produce plastic parts?
1. Extensive features and sophisticated geometry
The process subjects the injection mould to exceedingly high pressure, which presses the plastic available on the mould harder than any other moulding method. The high pressure allows the addition of detailed features into the part’s design. It also facilitates design and manufacture of complex shapes in a simple and affordable way.
2. High level of efficiency
Upon designing injection moulds as per the client’s specification and pre-programming the presses, the real moulding process is faster than other processes of moulding. Plastic injection moulding is quick and allows production of more parts from one mould. However, you need to outsource reliable plastic injection moulding services to obtain high-quality parts at pocket-friendly cost.
3. Automation to minimize production costs
Machines and robotics that can be controlled and managed by a sole operator are responsible for carrying out the injection moulding process. Automation reduces overheads significantly, which results in a reduction of overall manufacturing costs. The manufacturer can easily pass the cost saving made during the manufacturing process to the client.
What considerations should you make when selecting a plastic injection moulder?
With thousands of injection moulding companies available on the market, picking the best partner to assist you in mass manufacturing a product or an element of the product can be a challenging task. Make the following considerations before choosing an injection-moulding professional.
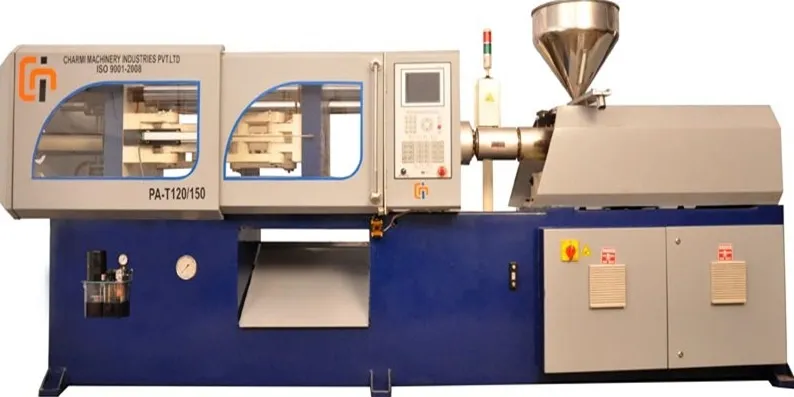