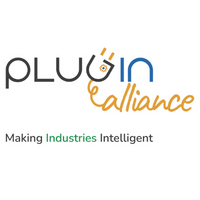
Plugin Alliance
View Brand PublisherCommunity Voices: How AI-powered CamCom helped a car manufacturer identify defects with its computer vision stack
CamCom deploys bespoke rigs with machine vision camera and lighting, and proprietary software, for micro-level defect inspections to remove subjectivity and bring efficiency to the quality check process.
It is no secret that industry 4.0 is an imperative now for manufacturing anywhere in the world. The pace of standards adoption has grown multifold. With memories of the pandemic and the consequent disruption still fresh in our minds, it is only natural that industries look at future-proofing themselves wherever possible.
As many as 63% of products in the world are made from metal, plastic, and/or glass. Quality inspection in an automobile production or manufacturing facility is a tedious and inefficient task. It tends to be labour-intensive and subjective, slow, and prone to error.
Ajith Nayar, Umesh, and Mahesh Subramanian started CamCom in 2017 to solve this very problem. The Bangalore-based company is an award-winning, industry-agnostic, AI-powered platform for visual inspections built on a computer vision stack.
The trio had noticed that while computer vision as a technology was present in labs, not everyone had access to it. “We wanted to democratise it. Much like any decent startup, the idea was broached and refined over many Old Monks in bars and pubs across Bangalore,” they said.
“It is natural that industries look at future-proofing themselves so operations are not impacted. Automation, digitisation, and digitalisation are the norm. Our platform is an integral part of this journey,” they added.
The growth journey
CamCom deploys bespoke rigs with machine vision camera and lighting, and proprietary software, for micro-level defect inspections to remove subjectivity and bring efficiency to the quality check process. The results are better, standardised quality reports with a faster turnaround.
Their AI-powered superfast micro-defect inspections and analytics offer a real-time pass/fail control, and the visibility to optimise the overall process. These inspections create a digital passport of the vehicle’s condition for Finished Vehicle Logistics (FVL). Through it, suppliers and original equipment manufacturers (OEMs) can trace and address the root cause to avoid costly recalls.
CamCom’s platform is used by many industries and government agencies. It enables auto OEMs to increase defect spotting by 55% with RCA analytics.
The CamCom edge
A recent example that showcases the quality of work is when the team worked with a customer seeing a high rejection rate in their car assembly unit. This was due to quality issues in their paint and assembly lines. The manual quality check, at two minutes, per car was inefficient and slowed the production line.
The customer also had issues with late rejection at the assembly stage for components that had defects after quality checks. These late rejections reduced the overall production of automobiles.
To resolve these problems, CamCom did micro-level defect inspections using bespoke rigs with machine-vision cameras and controlled lighting. Images were captured using cameras on rigs, and processed to identify and label defects.
A real-time pass/fail control optimised the process. Vehicle movement was controlled with an automated assembly system based on a programmable logic controller (PLC).
The processed images were further fine-tuned with analytics and pass/fail results were published on a centralised dashboard.
The impact
CamCom’s efforts helped the customer distinguish an actual defect from an acceptable variation, catching defects up to 50 microns. It led to increased productivity and efficiency by freeing up quality inspector time from manually checking for defects. Multi-stage checks eliminated seepage of a defective automobile into the market. Analytics on defects enabled root cause analysis so that the reason could be identified upstream.
Plans for the future
CamCom is a 49-member strong team with offices in Bangalore and the UAE.
“COVID put our plans for international expansion in US and Europe off by two years. We are now making up for that,” Nayar said. The company is eyeing international expansion with offices in the US, Europe, and Southeast Asia this year.
The team also wants to roll out the CamCom Vision platform, a low-code, no-code platform that can help create models quickly using transfer learning from existing models.
“We are also working on a dedicated vision lab in the US,” Nayar said.
About Community Voices
Community Voices is a series of articles from the Plugin Alliance that spotlights solutions and startups helping India’s manufacturing and supply chain industries benefit from smart technology. The series leads into Innovent 4.0, an exclusive industry technology conclave from the Plugin Alliance — a first-of-its-kind Industry 4.0 alliance in India — with the aim to showcase India’s role in the Fourth Industrial Revolution. In tune with the event, the series will continue to highlight stories from Industry 4.0 startups.