Nova Formworks’ decade-long journey to making construction as easy as building legos
To combat problems with steel and plywood formworks in construction, Vikas Mittal introduced plastic formworks in the market making construction a simple process.
For some, the early 2000’s is a time when the real estate market was booming. Until the financial crisis in 2008, the sector saw annual growth of 30% in India.
During this time, formworks—structures designed to keep cement in place still it turns solid—were made with plywood and steel. Vikas Mittal, a plastic manufacturer in Delhi, was among the first to notice the shortcomings of these methods.
Though not an engineer, Mittal understood the ways of the industry quicker than others owing to the time he spent around his father, Jagdish Rai Mittal, who had a plastic manufacturing business in Bengaluru.
In 1970s, Rai ran a cable manufacturing company in Delhi. In 1976, he relocated to Bengaluru and set up a PVC pipe manufacturing company, subsequently expanding into plastic compounding in the 1990s called Wonder Moldplast.
“When I visited the factory, my father always used to keep me on the work floor and never in the office,” Mittal recalls.
The experience on the floor eventually helped him later on, when he joined his father’s company in the '90s and took charge of the factory independently—eventually diversifying into plastic molded furniture and setting up a factory in Ghaziabad.
Eventually, Mittal was eager to tap into the use of plastic in construction. This is when he set up Nova Formworks Pvt Ltd and hasn't looked back since.
Finding a viable solution
Structures that were used to make buildings back in 2005 needed a number of workers which often led to increased labour costs. Mittal chose to address these issues by introducing plastic as a material for formwork construction beginning with a plastic ply offering in 2015.
However, this product lacked durability—it lacked a locking system and the polymer was not strong enough to retain its shape with changing temperatures of cement.
“In 2011, after years of research and redesigning efforts, we developed a comprehensive formwork system with a secure locking mechanism which we patented,” said Mittal. “This locking system ensured a leak-free construction process. It was lightweight and could be used multiple times.”
This, Mittal attributes to his experience in plastic compounding which helped in increasing the strength of the polymer.
As per Mittal, Nova Formwork’s products are easily assembled and removed—almost like lego blocks, making it easy for anyone to use it. "Even an unskilled labourer can easily use it. It potentially reduces the overall labor force required for a project," says Mittal.
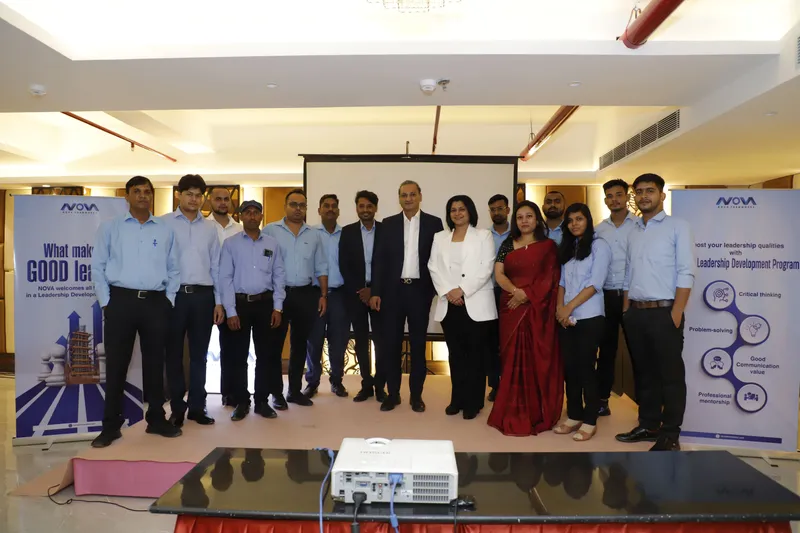
Nova's team
In 2021, Nova Formworks was recognized as the best company in the scaffolding and formworks category (small) by CIA World Awards. It has two manufacturing units in Bengaluru and Delhi with a team of 200 people.
As per Mittal, it has no direct rivals in India but finds competition in Slovenia, Indonesia, and China.
At first, collaborating with bigger companies and builders accepting of its products was critical for Nova Formworks. During 2013-14 when the real estate industry was facing a slowdown, medium and small-scale contractors as well as builders grew cautious about adopting a new product.
“They were hesitant to believe that plastic formwork could effectively replace traditional materials like wood or steel,” says Mittal.
On the contrary, larger contractors such as L&T, Shapurji Pallonji, Ahluwalia, and Tata Projects were willing to explore the company’s products.
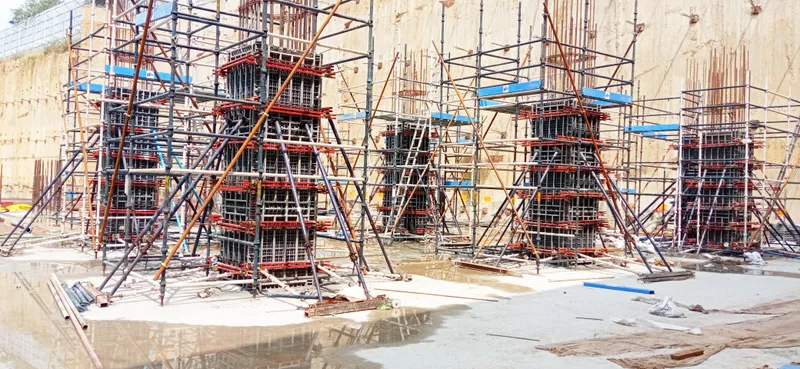
Once the pandemic hit and it brought on labour shortages, the need for innovative products arose again—giving Nova Formworks’ products greater market acceptance. This eventually translated to good business over the last three years. Their client base grew significantly from the 15 businesses it was serving earlier.
The company’s revenue grew from Rs 22 crore in FY21 to Rs 41 crore in FY22. Most recently, it made Rs 62.5 crore in revenue in FY23.
The sustainability question
While plastic may have a reputation for being non-eco-friendly, Nova Formworks is firm that its products stand out due to its ability to be reused multiple times. "One of our customers in Chennai mentioned that they've used it for 400 times," says Mittal.
For a quick comparison, steel formworks in construction can be used 30 to 40 times, and the plywood ones is limited to 5 to 6 uses. While steel can be recycled, it can be an expensive process.
Besides reusability, Nova Formworks offers a 25% replacement value to its customers. For every four used panels they return, they can obtain one new panel.
Despite being 3.5 times more expensive than plywood, Nova's formworks, priced at approximately Rs 6000 per square meter, offer a significantly higher repetition rate. It is easier to work with and reduces labor costs, ultimately leading to faster project completion.
The company also recently introduced a monolithic system within its plastic formwork offerings, a format which is currently treding in real estate. A monolithic system refers to a method where a single formwork system is employed to cast walls, slabs, columns, and various structural elements simultaneously in.
In addition to working in the real estate sector, Nova Formworks also contributes to infrastructure projects for timely completion. It recently deployed its formworks for the construction of underpasses along the Dwarka Expressway in New Delhi for the G20 summit, which required to be constructed fast.
It is also looking to expand its international presence and has started exporting to countries like Zambia, Western Africa, the UAE, Bhutan, Bangladesh, and Malaysia.
Edited by Akanksha Sarma