How industrial robots that can ‘see’ and ‘understand’ can improve ROI
Industrial robots must be product-agnostic with adaptable robot arms so that the it can be considered an essential asset with a 10-year ROI, irrespective of product type, design, or customer.
Henry Ford’s “You can have any colour as long as it’s black” manufacturing style is long gone. Our era of hyper-consumerism means manufacturers need to innovate and update product pipelines much faster. This demand drives the need to invest in better automation to streamline global supply chains, improve quality control, and stay competitive in a fast-paced global market.
But manufacturers today are faced with a peculiar Catch-22 situation when it comes to investing in automation.
Would you buy a washing machine if installation and maintenance costs comprised 70-80 percent of the total cost of ownership, and the device itself a mere 20-30 percent? Let’s assume that you need it, so you buy one.
Now, what if you find out that within two years, your machine cannot wash the majority of your clothes without an upgrade and another expensive installation? Would you consider this a sound return on your investment?
Your answer is surely a resounding no.
Unfortunately, in the world of industrial robotics, this type of situation is a reality. Buying an industrial robot arm is a large investment. However, 70-80 percent of the total upfront costs are from customised end-of-arm-tooling, part-specific structuring mechanisms, tedious calibration, custom software development, and systems integration. The reusable component, the robot itself, is only 20-30 percent of the cost.
Manufacturers need product designs to stay the same for at least five to seven years post-purchase to achieve a return on their investment (ROI). However, in today’s world of ever-shrinking product lifecycles, that is no longer guaranteed.
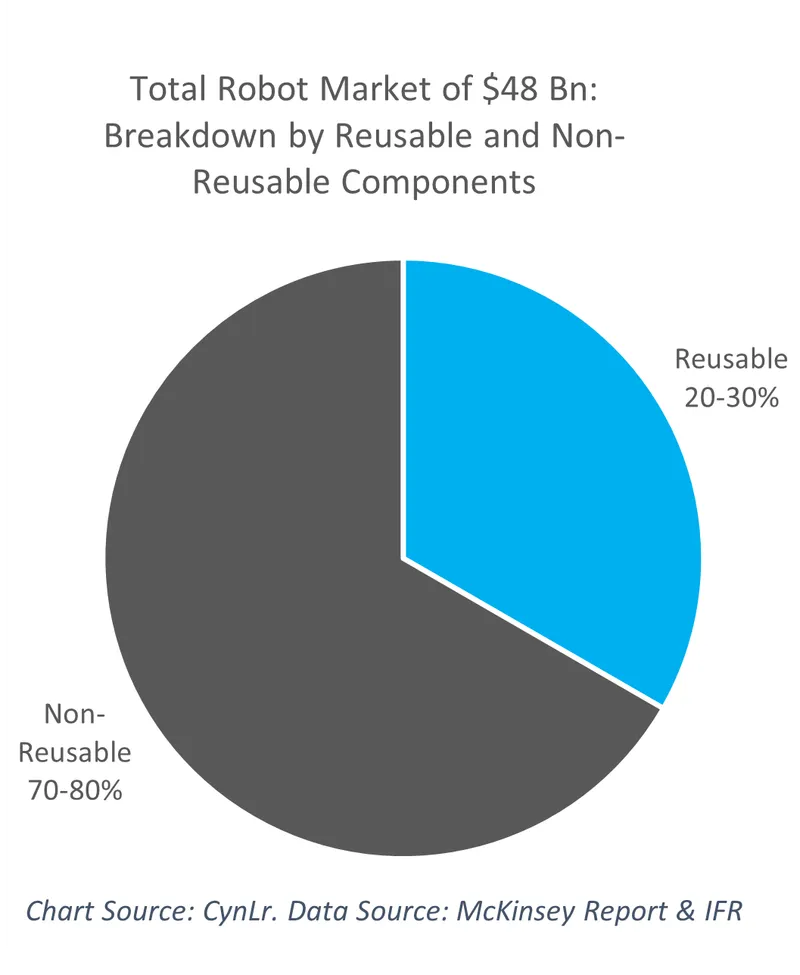
Manufacturers need to rely on the value that industrial automation brings. But any investment is guided by the fundamental desire to gain returns on that investment. And herein lies the crux of the issue. Today’s automation does not permit the level of agility required to survive in a fast-changing world, which introduces more uncertainty when evaluating ROI.
More automation, more benefits
While ROI estimates are largely economic, many other factors drive the need for industrial automation. At its core, the guiding principle of mass manufacturing is creating the same products repetitively while lowering the costs required to produce them. And indeed, cost reduction is the top driver for investing in industrial automation (McKinsey report).
A close second is quality control. This is especially true in industries where consumers care about a final product’s quality - like in automobiles, airplanes, medical devices, and children’s products.
For example, if I drive a Toyota car, Toyota is ultimately responsible for the quality of the car. But there is an entire chain of components that make a final product. This ecosystem is also accountable for the quality of their products. As a result, Toyota’s strict quality control measures extend beyond their factories, all the way down their supply chain.
So, if smaller parts manufacturers want to build and retain the trust of a larger manufacturer like Toyota, an investment in automation demonstrates a commitment to greater quality control. This focus on quality becomes a competitive advantage to acquire more business and lower expensive insurance premiums.
Automation is also necessary for specific tasks that are hazardous for humans to perform, particularly on a repetitive basis.
For example, magnetic particle inspection involves inspecting items under a UV light. This process, though commonly used, is extremely strenuous for the human eye. Every critical metallic object that is manufactured (like engine parts) goes through this type of inspection to ensure quality. But although unsafe for humans, there is no automation solution readily available yet as a substitute.
So, more automation is essential. And there is active investment in industrial automation – the global industrial robotics market is an estimated $16.2 billion for just the robot component with a 14 percent CAGR (IFR World Robotics, 2018). The total market is $48 billion when all auxiliary services and products are included. But how can we help more manufacturers, even mid-sized and small, make larger investments in much-needed automation with the confidence that they will reap higher returns on their investments?
Need to increase automation ROI
Currently, even small design changes to a product require expensive re-installation, redesign of end-of-arm tooling, re-calibration, and software overhauls. Only the robot or robot arm (20-30 percent of the original costs) is reusable. ROI calculations then become like walking a tightrope.
A cost-effective solution to this issue can revolutionise the entire field of manufacturing - even in industries where trends change so fast that only manual labour can currently keep up. Imagine being one of the go-to manufacturers for the shell of the latest Samsung Galaxy phone.
The next version of the phone is sure to be drastically different. Global trends may dictate that new models need to be half the width of their predecessors. Also, the new version may need to be released within a year of the previous one. Only those who can quickly adapt can succeed in such an environment.
Another benefit of this flexibility will be the ability to better comply with changing regulations. In India, the Supreme Court decreed that BS6 emission standards must be followed. These standards were designed to reduce harmful emissions from automobiles significantly. However, the switch from the previous standard BS4 to BS6 has been an on-going five-year project. This is because critical components and processes had to change and this is cumbersome and expensive.
But with greater flexibility, this whole process could have been much faster. The automotive industry would have been able to cost-effectively and quickly adapt. The most significant benefit from faster BS6 adoption would have been for us to have breathed cleaner air much sooner. This is why adaptable automation and the manufacturers that invest in it will emerge the clear winners going forward.
Higher returns on robots: the vision
What if you had to invest in robotics, and 70-80 percent of your original investment is in re-usable components, and only 20-30 percent is in application-specific customisations or services. And not just in the short term, but over a longer duration too. Doesn’t the ROI on this investment sound much better?
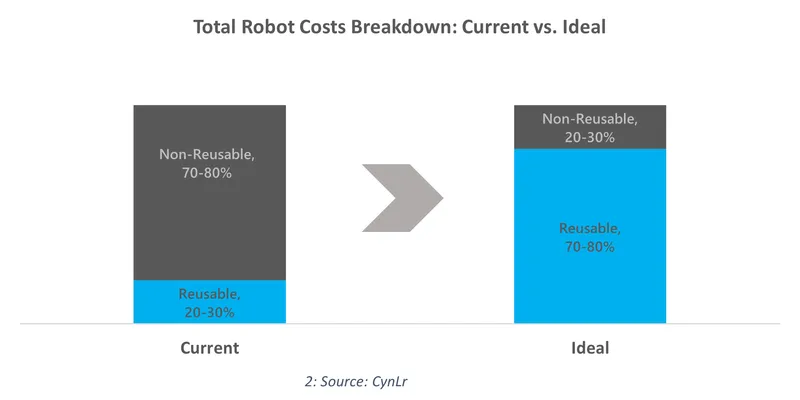
Minor changes in product design should not have to disrupt entire operations and involve massive costs. Industrial robots will have to be product-agnostic.
Ideally, robot arms must be easily adaptable so that the robot itself can be considered an essential asset with a 10-year ROI, irrespective of product type, design, or customer.
This level of flexibility allows manufacturers a tremendous level of freedom. Robots will no longer be product or task-specific but an integral part of a factory’s infrastructure. For this, robot arms will need to learn how to “see” objects and “understand” tasks, similar to humans. Robots will have to locate a specific object from a bin regardless of orientation, pick it up, re-orient it as required, and place it accurately in its destination. And any small changes in design or task must be easy and cost-effective to implement.
This agility requires significant breakthroughs in machine vision technology, which can unlock immense opportunity for the factories of the future when combined with a robot arm.
The robot manufacturing industry must step up and offer flexible solutions to empower manufacturers. More will be willing and able to invest in intelligent, adaptable robots while maximising ROI and realize the holy grail of manufacturing - hyper or fully-automated cost-effective factories.
Edited by Teja Lele
(Disclaimer: The views and opinions expressed in this article are those of the author and do not necessarily reflect the views of YourStory.)